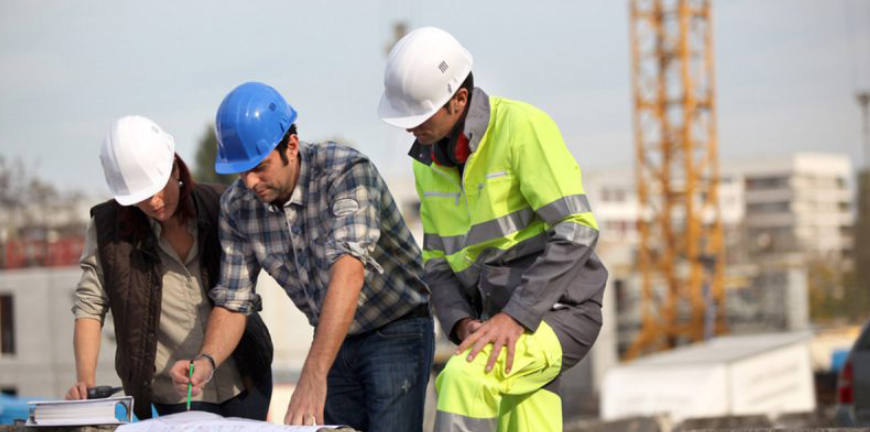
MEP ESTIMATE
Mechanical & HVAC Estimate:
Mechanical and HVAC estimate is a crucial process in construction projects that involves accurately estimating the materials, equipment, and costs required for the mechanical systems and HVAC (Heating, Ventilation, and Air Conditioning) installations. This estimate encompasses various components such as HVAC units, ductwork, piping, insulation, controls, and associated accessories. The estimation process begins by analyzing the project’s specifications, architectural and engineering drawings, and understanding the specific requirements for heating, cooling, and ventilation. Factors such as building size, occupancy, climate conditions, and energy efficiency goals are considered during the estimation process. Accurate calculations are performed to determine the appropriate sizing and quantity of HVAC units, ductwork lengths, pipe sizes, insulation thickness, and other materials. The estimate also includes labor costs, taking into account the complexity of the installation, the number of skilled technicians required, and the necessary equipment and tools. A detailed estimate report is generated, outlining the quantities, costs, and specifications of all the components, providing a comprehensive plan for the mechanical and HVAC systems. This estimate report serves as a valuable reference for budgeting, material procurement, and project planning, ensuring the efficient and effective functioning of mechanical systems and HVAC installations in the construction project.
Electrical Estimate:
Electrical estimate is a critical aspect of construction projects that involves accurately estimating the materials, equipment, and costs required for electrical systems and installations. This estimate encompasses various components such as wiring, lighting fixtures, outlets, switches, panels, conduits, and associated accessories. The estimation process begins by analyzing the project’s specifications, architectural and engineering drawings, and understanding the specific electrical requirements for power distribution, lighting, and safety. Factors such as building size, occupancy, electrical load calculations, and electrical codes and regulations are considered during the estimation process.
Accurate calculations are performed to determine the appropriate sizing and quantity of wiring, conduits, panels, and other electrical materials. The estimate also includes the selection and calculation of lighting fixtures, switches, outlets, and other devices based on the project’s lighting design and electrical layout. Additionally, considerations for safety devices such as circuit breakers, ground fault circuit interrupters (GFCIs), and surge protection are taken into account.
Labor costs are an essential component of the electrical estimate, considering the complexity of the electrical installations and the number of skilled electricians required for the project. The estimation process considers the time required for installation, wiring, connections, testing, and any specialized equipment or tools needed.
A detailed estimate report is generated, outlining the quantities, costs, and specifications of all the electrical components. This report serves as a comprehensive plan for budgeting, material procurement, and project planning. It ensures the proper installation and functioning of electrical systems, compliance with electrical codes and safety standards, and the reliable and efficient supply of power throughout the construction project.
By conducting a thorough electrical estimate, contractors and project managers can ensure the accurate allocation of electrical materials, control costs, and deliver successful electrical installations that meet the project’s requirements and provide a safe and functional electrical system.
Plumbing Estimate:
lumbing estimate is a crucial aspect of construction projects that involves accurately estimating the materials, equipment, and costs required for plumbing systems and installations. This estimate encompasses various components such as pipes, fittings, fixtures, valves, water heaters, pumps, and associated accessories. The estimation process begins by analyzing the project’s specifications, architectural and engineering drawings, and understanding the specific plumbing requirements for water supply, drainage, and gas systems.
Accurate calculations are performed to determine the appropriate sizing and quantity of pipes, fittings, and fixtures based on the plumbing design and layout. Factors such as building size, occupancy, fixture counts, plumbing codes, and regulations are considered during the estimation process. Additionally, considerations for water heaters, pumps, and other plumbing equipment are taken into account.
The plumbing estimate also includes labor costs, considering the complexity of the plumbing installations and the number of skilled plumbers required for the project. The estimation process takes into account the time required for pipe installation, connections, testing, and any specialized equipment or tools needed.
Other costs such as drainage systems, venting, insulation, and backflow prevention devices are also accounted for in the plumbing estimate. It is important to consider any specific requirements for water conservation, energy efficiency, or sustainable plumbing practices.
A detailed estimate report is generated, outlining the quantities, costs, and specifications of all the plumbing components. This report serves as a comprehensive plan for budgeting, material procurement, and project planning. It ensures the proper installation and functioning of plumbing systems, compliance with plumbing codes and regulations, and the reliable and efficient flow of water and drainage throughout the construction project.